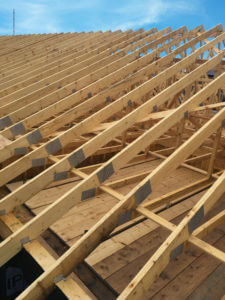
Andrew Orriss at the Structural Timber Association takes an in-depth look at the role of structural timber systems in housebuilding and how they can help achieve faster build times, lower embodied carbon and more energy efficient homes in line with current standards as well as the Future Homes Standard.
Timber is a material that has been used for structural purposes in construction for centuries, especially in housebuilding, but has seen more and more competition in recent decades from other construction methods and materials. However, there is now growing pressure to combat climate change and achieve the Government’s net zero by 2050 target. The focus now is on both in-use carbon, the emissions related to energy usage, and embodied carbon, the total carbon associated with the production of the materials and construction of the building. Structural timber systems offer clear sustainability advantages as well as the versatility, flexibility and speed of construction that they can deliver.
The main structural timber systems are timber frame, structural insulated panels (SIPs), cross-laminated timber (CLT) and glued laminated timber (Glulam).
Timber frame
Perhaps the most widely known and understood is timber frame. In housebuilding, there is a long history of using this approach. However, its adoption varies in the UK. It accounts for around 24% of new build homes across the whole country but in Scotland around 90% of homes are built using timber frame compared with just 10% in England.
There are broadly two types of timber frame – open and closed panel. Open panel systems are structurally engineered panels that form the inside load-bearing leaf of the external wall, comprising studs, rails, sheathing on one face, and a breather membrane. Closed panel systems have the same basic structure but also include insulation, a vapour control barrier on the warm side and linings on the interior face. Closed panels may also include fitted windows and internal service zone battens for ease of construction.
SIPs
Structural insulated panels (SIPs) are factory manufactured panels that consist of an insulating foam core sandwiched between two structural facings – typically oriented strand board (OSB).
SIPs deliver excellent structural and thermal performance and can be fabricated to fit nearly any building design. The result is a building system with a high strength to weight ratio that is highly airtight and energy-efficient, quick to construct and which can be used in walls and roofs of residential properties.
CLT and Glulam
While currently used less frequently in housebuilding, cross-laminated timber (CLT) and glued laminated timber (Glulam) are valuable systems for certain types of development. CLT is a structural solid wood panel product that can be used to form wall, roof and floor sections. It is produced by stacking layers of timber, known as lamellas, at 90∞ to the layer below and glued together to create panels up to 24 metres in length and 2.95 metres in width. Similarly, glulam is an engineered structural beam created from layered parallel timber laminations. Glulam offers exceptional load-bearing capabilities and dimensional stability and can be used in various shapes with beams typically up to 50 metres in length and 4.5 metres in width.
Benefits of structural timber
One of the key benefits of structural timber is its sustainability, especially its low embodied carbon. It is estimated that the UK’s built environment is responsible for nearly half of the UK’s carbon emissions, and embodied carbon can account for as much as 30% of this. It is therefore essential that steps are taken to reduce the carbon impact of new homes.
Maximising the use of timber in new residential properties in place of other materials is a simple and effective way of achieving this reduction. Timber is a low carbon material due to the fact that trees absorb and store CO2 as they grow. Therefore, for every cubic metre of timber used in construction, 0.9 tonnes of CO2 is sequestered and stored for the lifetime of the building.
The timber used is responsibly harvested and sourced from farmed forests that are sustainably managed and properly maintained. In fact, typically for every tree cut, a further five are planted.
In addition, the production of structural timber systems has a relatively small carbon footprint as manufacturing the harvested timber into the structural components does not require energy intensive processes.
The other area of sustainability that is now a focus is energy efficiency, and here too structural timber systems can provide clear benefits. The Building Regulations that will be introduced as part of the Future Homes Standard will require homes built from 2025 to have a carbon footprint that is at least 75% less than one built to 2013 energy efficiency standards. This is in addition to the uplift in Approved Document L requirements that came into force in June 2022, which already requires CO2 emissions from new homes to be 30% lower compared to 2013 standards.
To reach these targets, a focus on delivering high levels of insulation and airtightness for new homes is necessary. Structural timber systems offer a simple route to achieving this as the use of both timber open and closed frame and SIPs offers excellent flexibility to increase the thermal insulation of the external wall construction. For example, closed panel timber frame systems can typically achieve U-values as low as 0.10 W/m²K. Additionally, the controlled factory conditions under which offsite systems are manufactured allows high levels of precision and means that when the panels are assembled on site, they form a highly airtight, energy-efficient building envelope.
Speed of construction
Finally, structural timber systems also deliver advantages to housebuilders with regard to the speed and reliability of construction. In fact, using a timber frame system can reduce the construction time by as much as eight weeks, when compared to other methods. One of the reasons for this is that the timber frame is produced offsite and delivered as prefabricated sections that can be erected within days. Additionally, because the fabrication takes place in a factory environment it is not impacted by the weather, reducing the risk of delays and ensuring a more predictable build schedule.
High quality structural timber systems have a vital role in lowering the embodied and operational carbon emissions of new homes as well as helping housebuilders to streamline construction on their developments. The STA is committed to providing confidence in structural timber systems across the construction industry. It does this through expert technical guidance, research, testing, education and training, backed by STA Assure – its unique Quality Assurance Scheme.
STA article