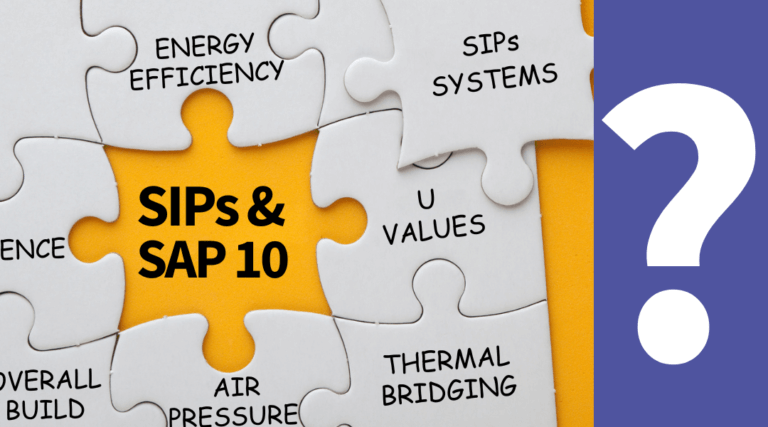
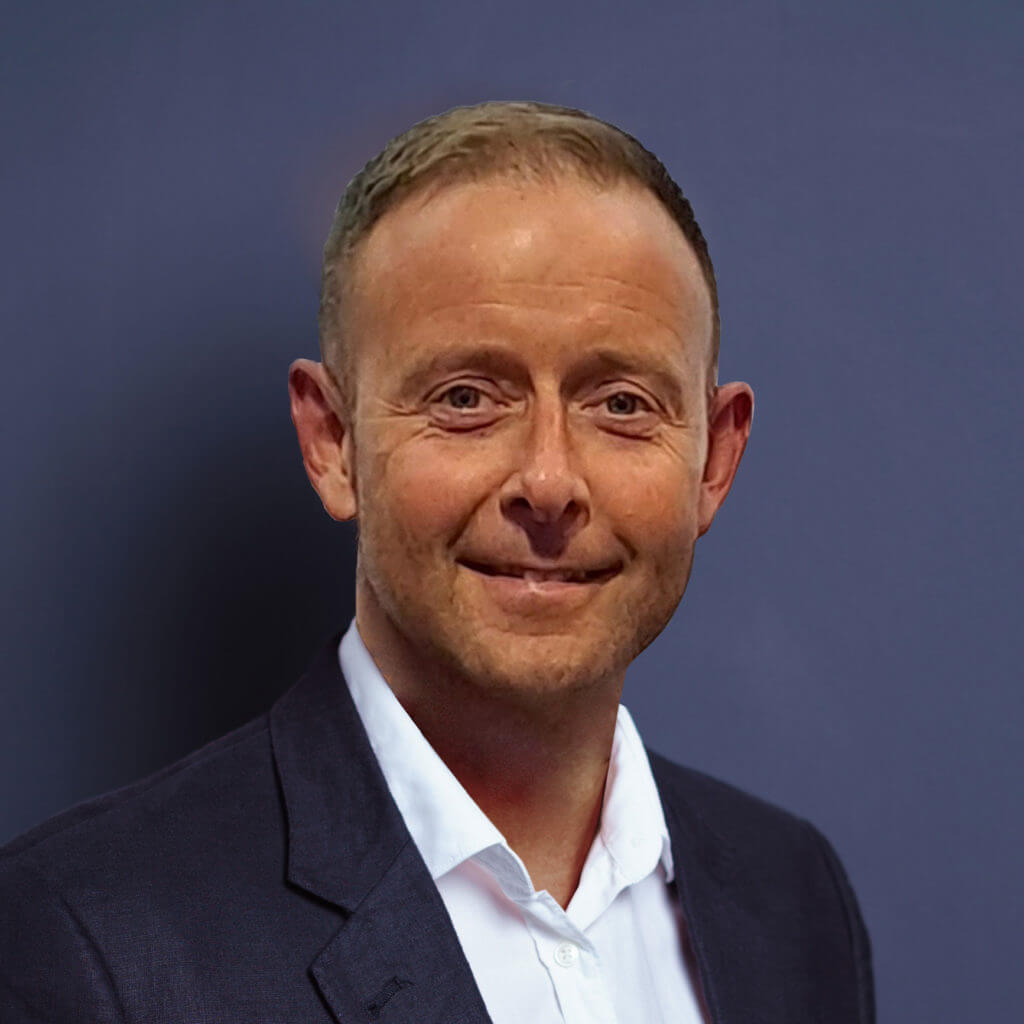
The use of SIPs now has a proven track record in the delivery of high performance, thermally efficient dwellings. Historically this was advantageous for our self-build clients that wanted to exceed regulations to drive down energy bills in their forever homes.
However, with regulations under Part L and SAP 10 becoming increasingly stringent the use of SIPs removes variables and provides a streamlined route to compliance for all.
Q&A's
Why do SIPs systems make this process easier for the client?
As building regulations continue to become more stringent, especially with amendments to Part L and now SAP10 as we move toward the 2025 future homes standard, the use of SIPs has huge benefits to all to ensure that compliance is achieved.
Being able to guarantee U values, provide thermal bridging details and help toward ensuring air pressure test results at early design stage allows all clients to accurately cost for the overall energy performance of their build or development.
Using back stop U values, Accredited Construction Details (ACD’s) and default Thermal Bridging (PSI) Values is no longer compliant so ensuring the overall energy performance of the build is achieving your requirements at the earliest stage is the best way to avoid further costs and delays to projects.
Can you expand on this regarding the U values, air pressure tests and thermal bridging - are your SIP panels compliant with current U Value Requirements?
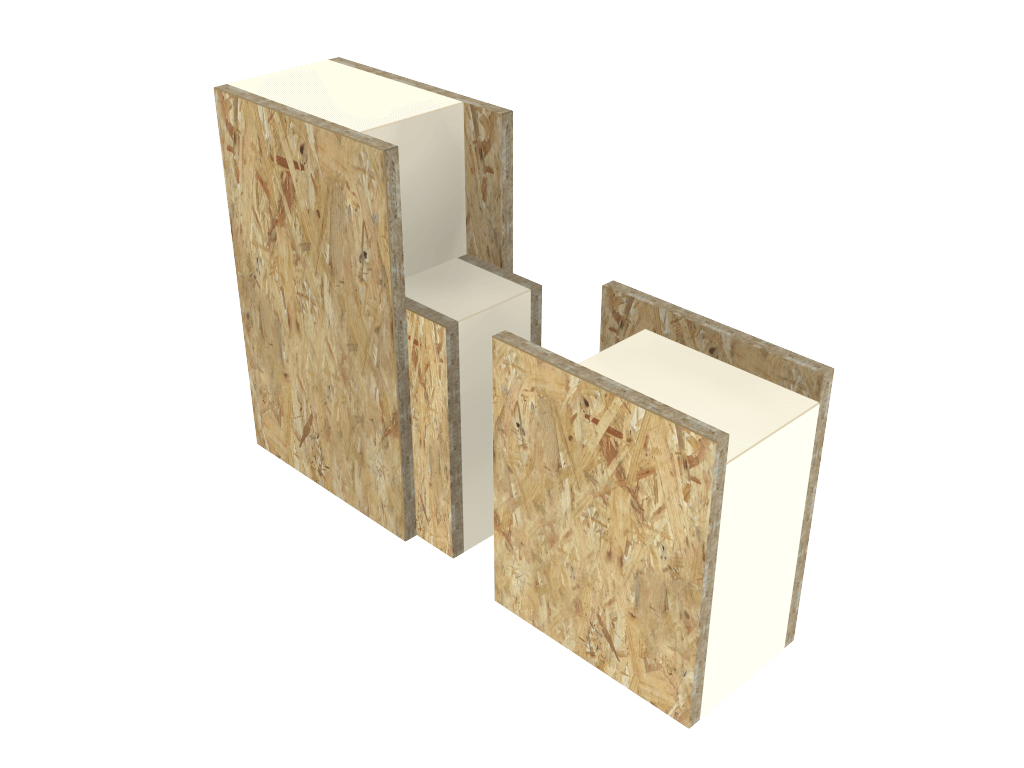
All projects must achieve certain U values to comply with current regulations. This is currently 0.18 in walls and 0.11 in the roof when looking at the target fabric energy efficiency of a dwelling.
However, depending on how the project is performing overall when considering additional measures such as Solar PV, Air Source heat pumps and MVHR it may be that the roof can be delivered at 0.13. Again, early modelling of the dwelling helps to confirm this which again shows the commercial advantage to having this done.
With our SIP systems we can complete U value calculations at the earliest possible stage to ensure we are achieving the required targets. With our SIP systems we are achieving these targets with the thinnest overall construction depths possible which maximises habitable or rentable space internally for the client.
Our range of SIP panels provide options as low as 0.11 in wall applications and 0.13 in roof applications depending on a project’s external finishes.
Along with U values, what is the importance of the Air Pressure testing?
There is no point delivering fantastic U values with poor air pressure test results! SIPs systems are inherently airtight given the accuracy of design, manufacture and install so our systems will often exceed current air pressure test requirements without additional measures. Obviously follow on trades must ensure they are sealing appropriately too around any penetrations made!
A significant change to the new regulations is that all plots on multiple unit developments must be air tested – even if they are the same house type. For developers, the worry of how each dwelling will perform can be eliminated when using SIPs which again reduces variables and potential costs if additional measures are needed due failed air pressure tests.
Our SIP systems also have minimal shrinkage and settlement in comparison to standard timber frame so this ensures air pressure test results are maintained through the lifetime of the building. This combined with reduced timber content in external walls also ensures that thermal bridging is kept to a minimum.
This leads nicely onto thermal bridging – what has changed under new regulations?
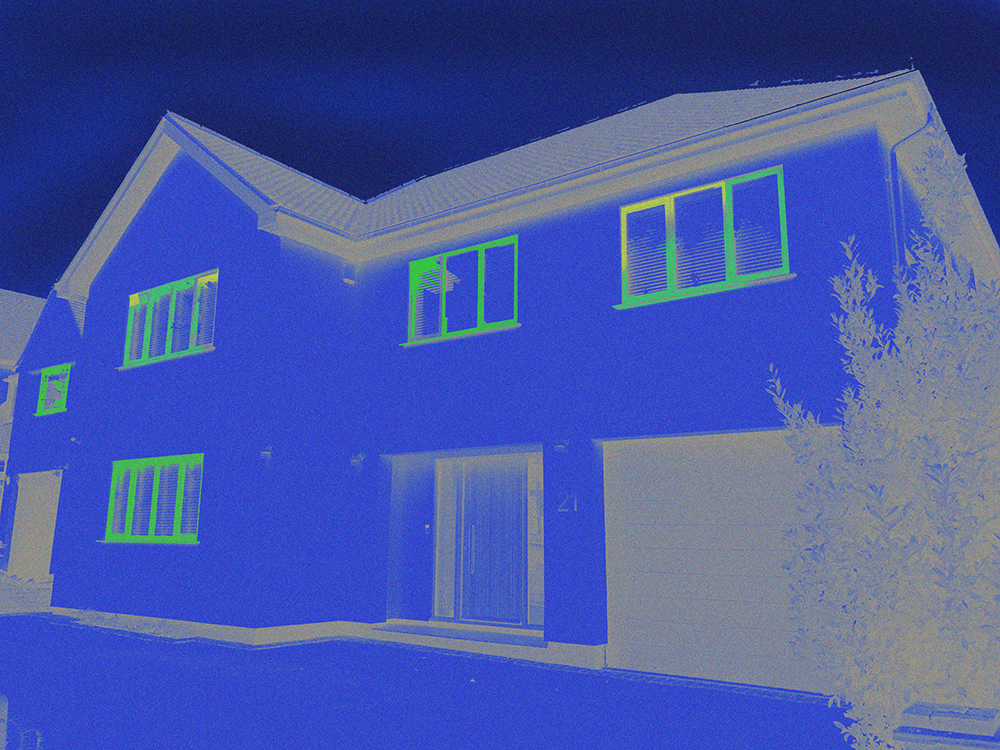
Default PSI values can no longer be used as this has a negative impact on fabric energy efficiency results, often leading to failure to comply.
Our SIP systems are complete with Pre calculated PSI values that can be sent to your SAP assessor along with the U value calculations we complete for you so the building fabric can be modelled at the earliest possible stage. This can then help to determine how your other potential measures such as MVHR, Solar PV, UFH and Air Source Heat Pumps will be incorporated.
This has certainly made the target fabric energy efficiency of the building a vital step in achieving SAP10 compliance.
Absolutely. The majority of our clients are looking to deliver thermally efficient, sustainable systems on time and on budget.
When you combine the predictability of cost, program time and thermally efficiency of our systems we are ultimately part of the process in providing our clients with a streamlined route to compliance at the earliest possible stage which further reduces variables and risk whilst on site.
The ability to ensure that a building will achieve the required energy ratings whilst still in design stage allows for all additional measures such as MVHR, UFH and Solar PV to be factored into the design and engineering process of our SIPs system.
As building regulations become more onerous under Part L and SAP10 and the demand for responsibly sourced, sustainable systems increases our BBA approved SIP panels and Structural Timber Association Gold standard certification ensures we are perfectly placed to meet the demands of our growing client base.
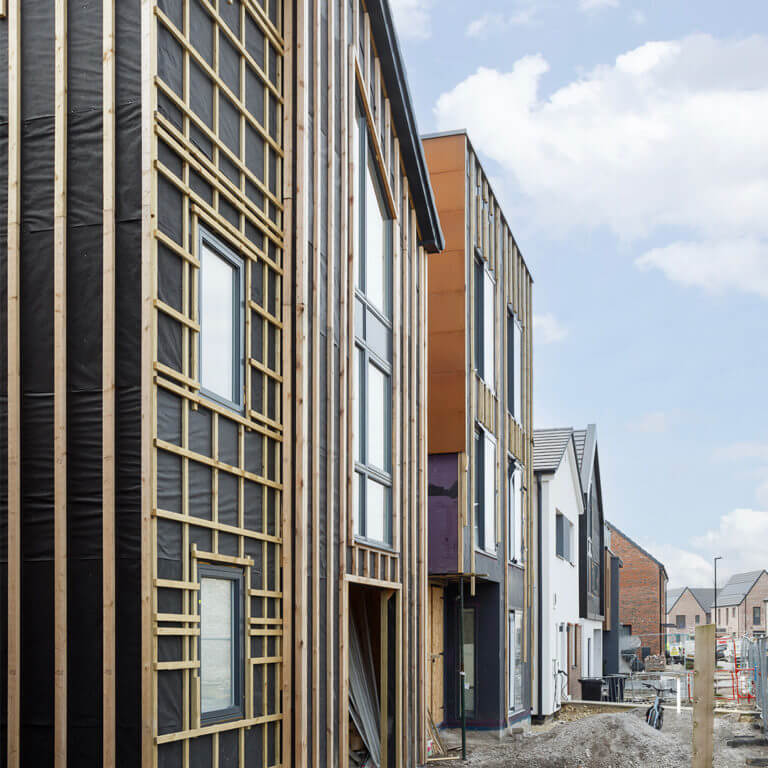
For more on SIPs you may like to read:
SIP Build UK Discusses the Future of Sustainable Buildings with Construction Update Magazine
NaCSBA Today, Hemsec and Sip Build UK form Partnership to Drive Energy Efficient Systems