Southend: SIP Self Build Home Project
About the project
ARCHITECT: S F - BDA
PROJECT TYPE: SIP Self build
System Products:
172mm SIP Panel
The panels are typically 1220mm wide and can be as long as 7.5 metres in length to suit each individual project. https://sipbuilduk.co.uk/sip-walls/
172mm SIP Panel
The panels are typically 1220mm wide and can be as long as 7.5 metres in length to suit each individual project. https://sipbuilduk.co.uk/sip-walls/
Press Web Internal Floors.
A pressweb floor is a type of raised access floor system made from modular steel and wood panels that provide convenient access to electrical and mechanical equipment.
Caberdeck
Caberdeck is a structural decking derived from CaberFloor P5, which meets the standards set out in BS EN312: part 5 and BBA-approved, offering additional confirmation of its quality and efficiency. https://sipbuilduk.co.uk/sip-flooring/
TF200
TF200 is a breather membrane product offered by the company Glidevale Protect. It is a high-performance membrane meant for safeguarding external walls including roof while construction is happening.
Architecturally Complex – tbc + *2016
The costs provided are totally indicative and should be used informatively and not part of any detailed budgeting process. How long is a piece of string comes to mind!!! https://sipbuilduk.co.uk/sip-cost/
We do hope however that this helps to provide a picture of what can be achieved with our structures within different budget ranges.
Southend – SIP Self Build Home Project | When Dave moved into a 1930’s three-bed detached house with his family he had plans to increase the size of his home by 150 per cent by adding an extension. But the further he got into the project the more he felt as if there were too many compromises, particularly around temperature control with trying to mix old and new.
After watching numerous home-building and renovating programmes he was inspired to demolish his existing home and embark on a four-bed new-build family home on which there would be no compromise.
He decided early on that bricks and mortar wouldn’t deliver the home of his dreams and didn’t want to go whacky, with, say hay bales. A lot of desk research and a few visits to home-building shows led him to SIPS.
He said: “As a construction method it is commonplace in US. I spoke to Chris at one of the shows and with the backing of the SIPs manufacturer it felt like a very secure choice for a new-build. A quantity surveyor friend and I visited the SIP Build site and had a tour of the SIPs facility to see what was involved, from drawings to completion and were impressed by the professionalism and experience of the SIP Build team.”
The original house was demolished in January 2016, groundworks started in February and the structure was watertight by the first week of May. The family moved into their new home in December 2016.
The home is a spacious four double-bedroom, detached home. “I wanted to create a feeling of space, it’s got a wide hallway from which you’ve got a long-distance view through living space to the bottom of the garden,” said Dave.
The combined living area has a galleried landing giving a feeling of height and space and two of the bedrooms have vaulted ceilings, one of which leads up to a mezzanine floor which takes up a third of the loft space. The vaulted master-bedroom includes a dressing room and en-suite. On the ground floor it has an integral garage and plant room, a cinema room, shoe and coat cupboard, utility room and pantry.
“The house works, when people com round they love the way it flows and the feeling of light and space we’ve created,” said Dave.
SIPs contributed to the success of the project because it delivered a ‘super-efficient’ home with precise, off-site manufacture that provided a watertight structure within six weeks. It also enabled Dave to pre-order windows and doors because he was confident the final measurements would be accurate, which reduced the build time.
Temperature control was another important feature in the design of the house, underfloor heating was fitted downstairs and in the tiled bathroom floors upstairs and a mechanical ventilation and heat recovery system was installed to extract warm air and deliver fresh air to the structure and regulate temperature throughout the house.
“The house is consistent, you’re not walking into one part of the house and thinking it is chilly, even if you open and close outside doors it is consistent”
Dave
Dave was so confident in the ability of SIPs to deliver the thermal qualities he required he didn’t install any additional heating upstairs, which also increased the internal useable space.
And nine south-facing solar panels provide energy and significant cost savings. During their first winter in the house the family didn’t require any additional upstairs heating and utility bills reduced by around 70 per cent in comparison to the costs for the original 1930’s house which was just 40 per cent of the size of the new-build.
Looking for More Inspiration?
Explore our self-build project gallery and see what’s possible with SIPs.
👉 View the Gallery ›
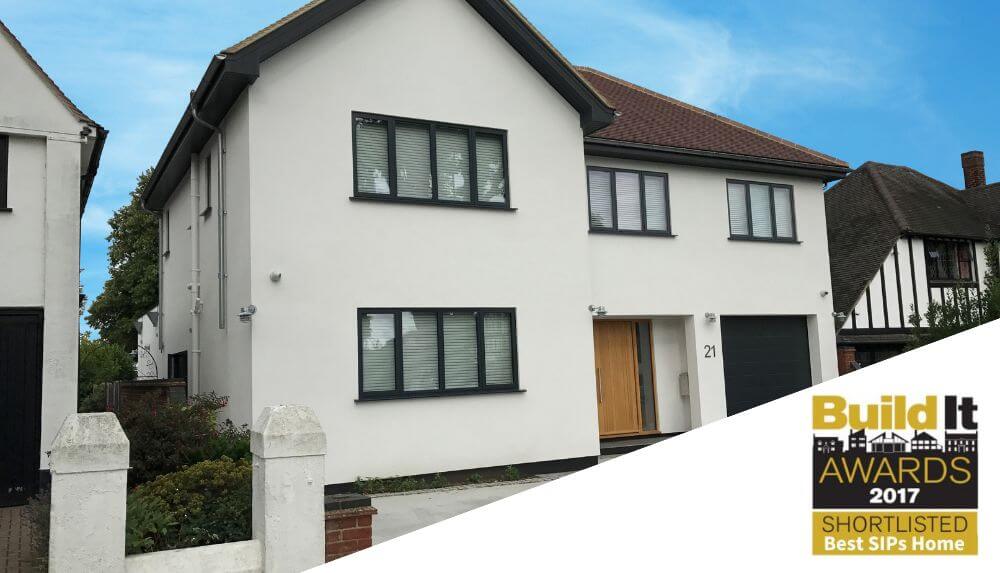
“I would wholeheartedly recommend Chris and the SIP Build team, and I have done. If I was building another house they would be my first port of call. I needed it to be right because it was my home and there was a vibe that built up throughout the build from Chris and his team in the office and the guys on site, they were all good people, really genuine, and couldn’t do enough to help. My wife was happy it was such a nice bunch of guys doing the build as well.”
Dave
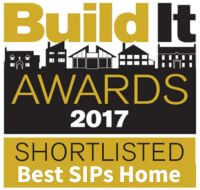