SIPS Specifications
Standard Details
SIP Specifications | Standard Details | Enter your email address for access to our Technical Downloads, We will use it for marketing purposes for Sip Build UK and not pass on to any third party or ever sell your personal information.
<<< Complete the form now and gain instant access to our SIP Standard Details.
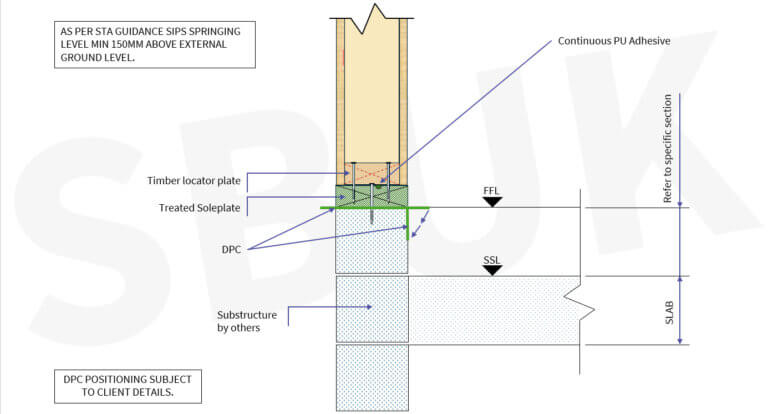
External Finishes and Rainscreen Claddings - Walls
As soon as possible after SBUK SIP panels walls have been erected, a breathable membrane, e.g. TF200, should be fixed directly to the panels. External cladding should be installed over the breathable membrane.
The following are examples of external cladding for walls:
- Outer leaf of brickwork / stone, ensuring a minimum 50 mm cavity is maintained between the breather membrane and the brickwork
- Lightweight render coating carried on calcium silicate board which is supported by min. 25 mm deep by 50 mm wide vertical treated timber counter battens
- Feather edge timber boarding on min. 25 mm deep by 50 mm wide vertical treated timber counter battens. (check with architect regarding use of Fire protection board/treatment behind the timber boarding)
- Wall tiling mounted on tiling battens which are supported by min. 25 mm deep by 50 mm wide treated timber counter battens
- Proprietary brick slip system supported by min. 25 mm deep by 50 mm wide vertical treated timber counter battens.
External Roof Finishes
Roof Finishes
Tiles
- Interlocking concrete tiles are large format and are generally the most cost effective
- Plain tiles may be concrete or clay and they cover an average of sixty to the square metre, and so have a consequential increased labour cost. Plain tiles are often used for tile hanging
Slate
- May be stone, quarried slate or man-made
- Man-made slates are available and are made from either fibre and cement or moulded with a mixture of slate dust and glass fibre resin
Fixing
- SIP Build UK houses can accommodate most types of roof covering. If you intend to use natural or man-made slate it is important that details are agreed prior to the structure construction
- Tiled roofs will require nailing according to the exposure rating and the manufacturer’s recommendations
As soon as the tilers have finished, decorate the facia and fix the guttering prior to the scaffolding coming down
Thermal Properties
U Value Table
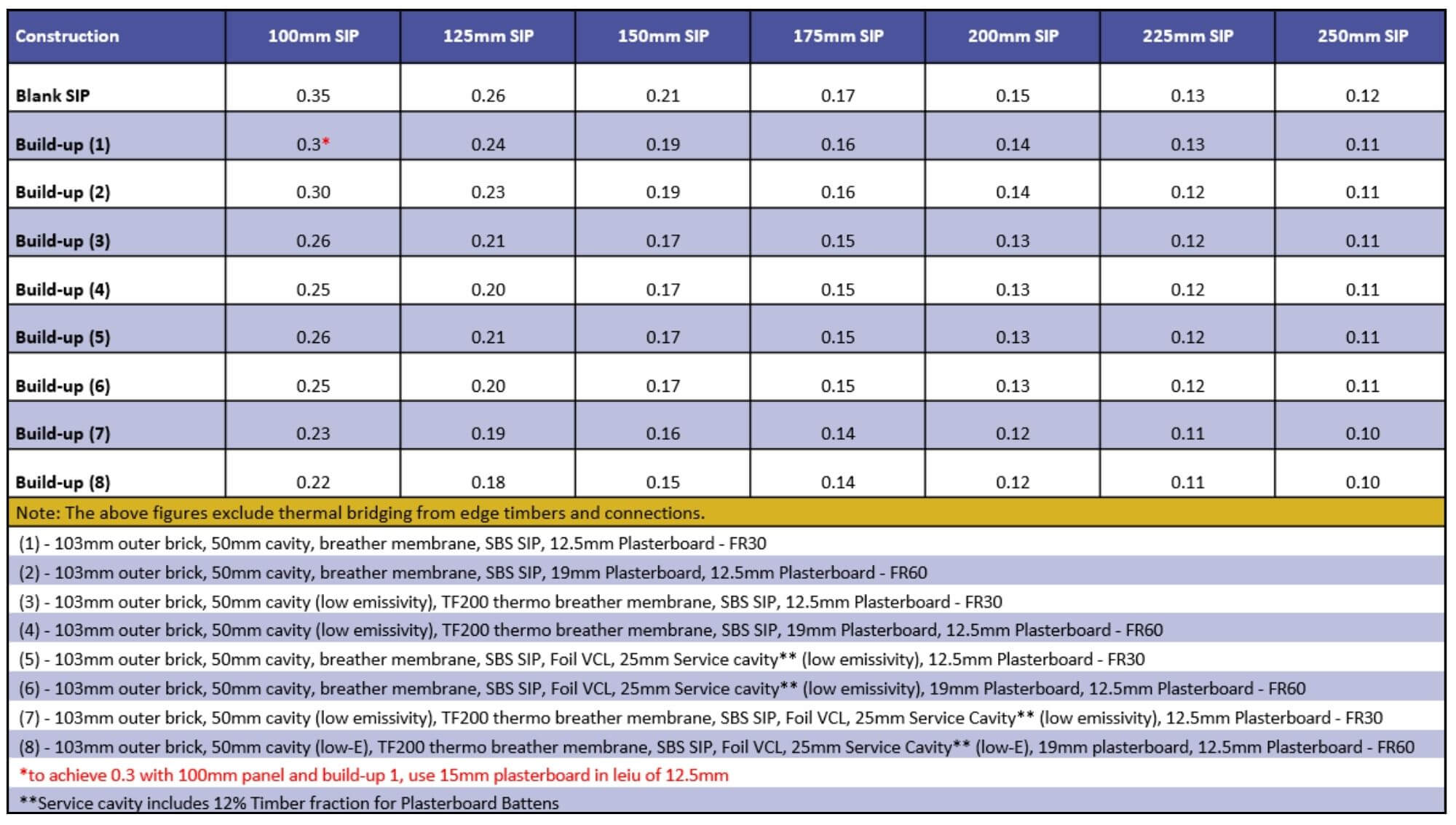
Air-tightness
In addition to the excellent U–values that can be achieved by walls and roofs constructed using the SBUK SIP panels the closed cell structure of the rigid urethane insulation core of the panels does not allow movement of air within them.
The insulation will not sag or physically deteriorate over time, as may be the case with other insulating materials.
Air leakage levels can be as good as 0.08 air changes per hour at normal pressures (approximately 1 m3/hour/m2 at 50 Pa). Standard results would be 3 air changes per hour. This is subject to the quality of the overall build.
The Facings
The SIPs panel comprises of BBA Approved 12mm Internal and 12mm External Oriented Strand Board (OSB)
grade 3 facings. OSB/3 has a thermal conductivity value λ of 0.13 W/mK.
Manufactured to specification EN 13986 and EN 300:2006, OSB/3 comprises of strands of softwood bonded
together using a formaldehyde free synthetic resin.
The OSB boards are responsibly sourced and comply to FSC and PEFC chain of custody requirements.
Further information and Certification can be obtained on request through SBS SIPs.
The Core
The core of SBUK SIP panels are a closed cell Polyurethane rigid foam system with zero Ozone Depletion Potential (ODP) supplied by BASF
Polyurethanes Europe.
The PUR core is CFC and HCFC free providing a < 5 value for GWP, as specified by various regulatory bodies.
Structural Dimensions
SBUK SIP panels are available in the following standard size(s):
- Panel Thicknesses – 125, 150, 175, 200 and 225
- Panel width is 1200mm as raw panel
- Lengths vary up to 7500mm.
ALL PROJECTS ARE CUT BESPOKE TO SUIT YOUR DESIGN.
Water Vapour Resistance
Assessed to be acceptable in relation to the intended use of the
building and any limitations regarding climatic zones
Durability
SIPs are manufactured from the highest quality materials, using state of the art production equipment to rigorous quality control standards, complying with ISO9001:2008 standard, ensuring long-term reliability and service life. SBS BBA Certificate
The panels will have comparable durability to that of OSB/3 to BS EN 300 : 2006, therefore, provided the installation remains weathertight and damp-proof; a life of at least 60 years may be expected. The long life expectancy of our product will reduce energy consumption of a building over its’ lifespan.
Resistance to Solvents, Fungi and Rodents
The rigid urethane insulation core is resistant to dilute acids, alkalis, mineral oil and petrol. It is not resistant to some solvent–based adhesive systems, particularly those containing methyl ethyl ketone.
Adhesives containing such solvents should not be used in association with SBUK Building System.
SBUK Building System components, which have been in contact with harsh solvents, petrol, mineral oil or acids, or components that have been damaged in any way should not be used.
The rigid urethane insulation core and facings used in the manufacture of SBUK SIP panels resist attack by mould and microbial growth and do not provide any food value to vermin.
Strength & Stability
The permissible vertical load resistance for SBUK SIP panels is sufficient for the System’s use as loadbearing partitions, separating walls, the inner leaf of external walls and pitched roofs in dwellings up to four storeys high.
Resistance to Airborne Sound
Weighted apparent sound reduction index for separating walls achieves a sound reduction of (Rw) of 44 dB
Weighted apparent sound reduction index for all other walls achieves a sound reduction of (Rw) of 37 dB
Fire Performance
Panel Internal and External OSB and CPB facings have Class 3 surface spread of flame to BS476: Part 7:
1987. When SBS SIPs are used as part of a through-wall build up they pass the requirements of BS476 Part
21 fire resistance of load bearing walls and have achieved up to 75 minutes fire rating. Non-Load bearing walls
can achieve up to a 90 minute fire rating (BS476 Part 22:1987).